Table of Contents
A 3D printing robot employs AI and machine learning
In a facility at the College of Engineering at Boston University, a robot arm drops tiny plastic objects into a precisely positioned box on the floor to collect them as they fall. These feather-light, cylindrical constructions, each no larger than an inch in height, fill the box one by one. Some are blue, purple, green, or black, while others are red.
Every item is the outcome of a robot autonomous experiment. The robot is looking for and attempting to create an object with the highest effective energy-absorbing shape that has ever existed on its own, learning as it goes.
The robot uses a 3D printer to build a small plastic construction, then measures and records its dimensions before moving it to a flat metal surface and crushing it with enough force to crush an adult Arabian horse standing on a quarter.
After that, the robot measures the amount of energy absorbed by the structure, observes how being squished alters its shape, and logs all of this information into a large database. After that, it cleans the metal plate and lowers the crushed object into the box, ready to print and test the next component.
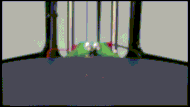
The robot’s computer algorithm will modify its design and size depending on all previous experiments, resulting in a very minor variation from its predecessor. This process is known as Bayesian optimization. The 3D structures improve in their ability to withstand the force of crushing experiment after experiment.
Keith Brown, an associate professor of mechanical engineering at ENG, and his colleagues in the KABlab made these tests possible. Since it was first conceived by Brown and his colleagues in 2018, the robot, known as MAMA BEAR (short for Mechanics of Additively Manufactured Architectures Bayesian Experimental Autonomous Researcher), has undergone modifications.
By 2021, the laboratory had programmed the device to create a shape with the highest mechanical energy absorption efficiency—a measure of how much energy it can absorb. Over 25,000 3D-printed structures have been produced in dozens of boxes during the course of this iteration, which has been running nonstop for more than three years.
Why are there so many different shapes? Anything that can efficiently absorb energy has a plethora of applications, such as providing padding for fragile devices being delivered internationally or serving as knee pads and wrist guards for athletes.
“You could draw from this library of data to make better bumpers in a car, or packaging equipment, for example,” Brown explains.
For the structures to function optimally, they must achieve the appropriate balance between strength and impact absorption. They cannot be so robust as to harm the objects they are intended to protect.
According to Brown, the finest structure that has ever been seen was only 71% effective at absorbing energy prior to MAMA BEAR. However, Brown’s lab witnessed its robot reach 75% efficiency on a cold January afternoon in 2023, shattering the previous record. Nature Communications has published the findings.
“We weren’t sure if there would be such a record-breaking shape when we first started,” says Ph.D. student Kelsey Snapp, who manages MAMA BEAR at Brown’s lab. “Slowly but surely we kept inching up, and broke through.”
With its four points, like slender flower petals, and dimensions greater than those of the earlier designs, the record-breaking structure defies the researchers’ expectations.
“We’re excited that there’s so much mechanical data here, that we’re using this to learn lessons about design more generally,” Brown explains.
Their copious data is already seeing its first practical use in the form of informing the creation of new helmet padding for soldiers in the United States Army.
In order to make sure helmets containing their patent-pending padding are comfortable and offer enough protection from impact, Brown, Snapp, and project collaborator Emily Whiting, an associate professor of computer science at BU College of Arts & Sciences, worked with the US Army and underwent field testing.
Compared to the record-breaking piece, the 3D structure used for the cushioning has a softer center and a shorter stature to improve comfort.
Brown has several autonomous research robots than MAMA BEAR. Other “BEAR” robots in his lab carry out various duties; one such robot is the nano BEAR, which uses atomic force microscopy to investigate the behavior of materials at the molecular level.
In addition, Brown has been collaborating with Jörg Werner, an assistant professor of mechanical engineering at ENG, to create a different system called PANDA, which stands for Polymer Analysis and Discovery Array. BEAR is designed to evaluate thousands of different thin polymer materials in order to determine which performs best in a battery.
Brown claims, “They’re all robots that conduct research.” “The philosophy is that they’re using machine learning together with automation to help us do research much faster.”
“Not just faster,” Snapp continued. Things that you couldn’t do before are now possible. We are able to accomplish a structure or objective that would not have been possible in the past due to the high cost and lengthy process.” Since the trials started in 2021, he has collaborated closely with MAMA BEAR, providing the robot with the machine vision. ability to see and clean its own test plate.
The KABlab aims to highlight the significance of independent research even further. Brown wishes to continue working with scientists from a variety of sectors that have a huge number of structures and solutions to evaluate. “We have no ability to know if we’ve reached the maximum efficiency,” according to Brown, thus even if they’ve already broken the record, they might do so again.
Thus, MAMA BEAR will continue to operate, pushing the envelope, as Brown and his team investigate potential uses for the database. In order to recycle the material for other tests, they are also investigating the possibility of unwounding and reloading the over 25,000 crushed bits into the 3D printers.
“We’re going to keep studying this system, because mechanical efficiency, like so many other material properties, is only accurately measured by experiment,” adds Brown, “and using self-driving labs helps us pick the best experiments and perform them as as fast as possible.”
read also : There are 15 jobs that are on the verge of extinction that you should avoid.
3D printing robot 3D printing robot 3D printing robot 3D printing robot 3D printing robot 3D printing robot 3D printing robot 3D printing robot 3D printing robot
1 thought on “A 3D printing robot employs AI and machine learning to produce a shape that is shock-absorbing beyond human ability.”