Table of Contents
Jet engines are sophisticated, costly devices that need to be handled carefully and maintained on a regular basis. While an aviation engine’s function of delivering power may be similar to that of an automobile’s engine, starting an engine is not the same as turning on the ignition in a car. Pilots have to follow a set of procedures in order to ignite a jet engine.
Pilots have certain checklists with them when starting engines. An onboard Auxiliary Power Unit (APU), a ground power unit (GPU) from the ramp, or cross bleed—air from another engine that is operational—are the three main sources of air used by the engine to start up. This article explores the fundamental idea behind jet engines, how they work, and the procedures involved in starting an engine.
The parts of a jet engine that are utilized during the first
In summary, the components of a standard jet engine are the intake, the compressor stage, the combustor, and the turbine stage. It functions a lot like an automobile’s engine does. The air is first brought into the intake and then compressed.
Air is sent from the compressor stage into the combustion chamber, where it is ignited and fueled, burning the air.
After that, the air is directed into the turbines and given room to expand. This expansion gives the flow more kinetic energy, and as it shoots out of the engine, the aircraft experiences an equal and opposite force. We refer to this as thrust.
The compressor stage must first be turned at a specific speed in order to pull air for the startup. The first prerequisite for starting a jet engine is this. A high bypass ratio jet engine features two compressor stages at its most basic configuration.
N1 refers to the low compressor stage and N2 to the high-pressure stage. Since the majority of engine accessories, such as oil and hydraulic pumps, are connected to the N2 compressor, it is this compressor that must be spun during the startup procedure.
The N2 compressor may be rotated using one of two techniques. One way is by the use of electricity. The majority of the time, turboprops and other smaller jet engines are started using this technique. In this instance, one of the engine’s electrical generators serves as a starter motor. It rotates when powered, and as it is geared to the N2 compressor, the N2 compressor also rotates as a result.
Larger jet engines use the second method. Here, the N2 compressor is turned on by a different starter motor. The motor is powered only by air and is referred to as an air starter. An Auxiliary Power Unit (APU) or a Ground Start Unit may supply this air.
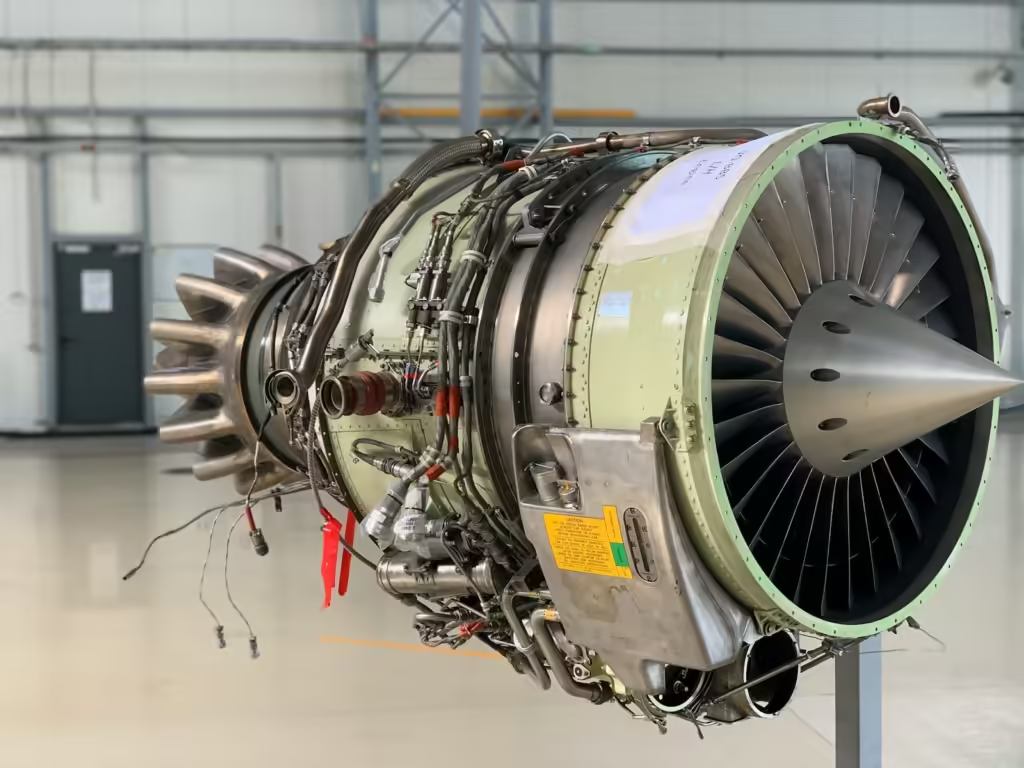
The initial process
As was previously mentioned, rotating the N2 compressor is required to start a jet engine. Sending air to the air starter motor is necessary for this to happen. This air, often referred to as bleed air, may be supplied by the APU if it is installed in the aircraft. The air conditioning units receive their air supply from the APU during ground operations. Nevertheless, the air to these devices is cut off at startup to free up air for engine starting.
The start valve opens when the pilot engages the starter, allowing bleed air to enter the starter motor’s turbine. The N2 is then turned by the starter motor. The pilot keeps an eye on this via the cockpit instruments while the N2 builds up. The pilot uses the fuel switches to add fuel to the combustion chamber at roughly 20% N2 rotation. The gasoline and air combination is subsequently ignited by the ignitors, raising the engine’s temperature. This temperature, known as the Exhaust Gas Temperature (EGT), is detected at the turbine stages or exhaust in the majority of jet engines.
When fuel is first added, the amount of fuel in the combustion chamber relative to air causes a significant increase in EGT. Less cooling results from less air. More gasoline is added to the engine as it accelerates, gradually raising the EGT. The engine eventually reaches a self-sustaining speed where it can accelerate on its own without the starter motor’s help.
At this moment, the igniters are turned off and the starter motor automatically uncouples from the N2 compressor. Once the fuel and air in the combustion chamber are balanced, the EGT peaks at a certain amount and then starts to decline. The starting process is now complete.
Peak EGT is a significant number. An elevated peak EGT may indicate engine deterioration. A problematic engine starter motor may possibly be the cause of this. In any case, extremely high peak EGTs at startup should be reviewed with maintenance to avoid escalation into more serious issues. The turbines’ temperature is indicated by the EGT itself, and as they are heat-sensitive, there is an initial EGT limit that should never be exceeded. Should this be surpassed, the aircraft should be turned over to maintenance and the engine should be turned down right away.
An aircraft can be connected to a ground start unit in the event that the APU is unavailable or unserviceable.
The adapter receives a long hose from the start unit that feeds air to the engines from the unit. When using this procedure, pilots utilize the start unit to start one of their engines at the gate. The engine is separated from the airplane as soon as it starts. The remaining engine(s) can then be started by diverting the air from the engine that has ignited through a cross-bleed valve. We refer to this kind of starting as a cross-bleed start.
The same procedure applies to engines that are started using a motor or an electrical generator; the only difference is that air is not needed during the startup. The only big airplane whose engine is started by electricity is the Boeing 787.
This uses a lot of power, and in the absence of an APU, the aircraft must be connected to two external ground power units in order to start the engine.
Problems with startup
In a jet engine, there are two primary start failures. A hot start is one thing, and a hung start is another. When fuel is introduced during a hot start, the EGT rises as predicted, but the temperature quickly rises to the start EGT limit. The pilots should turn off the fuel and ignition right away if this occurs. If this is delayed, the engine may become inoperable in a matter of seconds if the EGT limit is exceeded.
There is an easy explanation for a hot start. inadequate ventilation. This may be the result of a poor starter motor, an issue with the engine’s electronic control unit, or an inability of the APU or ground start unit to supply enough air. A hot start can also result from starting the engine in a strong tailwind since the wind prevents the engine from rotating.
In a stuck start, the engine compressor RPM is unable to increase to the self-sustaining speed or the anticipated value. The EGT is more than predicted given the low RPM, yet it is “hung” at an unacceptably low number. Closing the fuel valves is the first step in hung start engine shutdown. A hung start is primarily caused by a malfunctioning starting motor.
In the event that an engine does not start, the pilots had to perform a “blowout” cycle before trying again. This is because unburned fuel flooded the combustion chamber during the majority of unsuccessful starts. This fuel can ignite the flooded fuel and cause flames to shoot out of the engine exhaust if a start is attempted while it is in the chamber. This is referred to as torching or a tailpipe fire.
Engine parts are rarely damaged by torching. On the other hand, it can harm the parts of the aircraft that are in direct contact with it, such as the flaps and wings. The pilots must simply cut off the ignition and operate the starter motor without adding gasoline in order to complete the blowout cycle.
By doing this, extra fuel is blown out of the combustion chamber by forcing air through it.
The aircraft engine restarts
Jet engines are very dependable. Nevertheless, there remains a possibility of a malfunction. The pilots can restart the aircraft in midair if an engine gives out. An aircraft jet engine starts similarly to one that is stationary. One notable distinction is that the aircraft’s forward momentum activates the compressor on its own when in flight. We refer to this as windmilling.
The rotation speed increases with aircraft velocity. Therefore, if the engine is flown at a steady windmilling speed, it can be started in the air without the assistance of the starter motor. To get the N2 compressor to run at a reasonable speed below this point, air from the running engine or air from an APU may be needed.
read also: F-16XL: A ‘lost’ F-16 Fighting Falcon powered by steroids
read also: The smallest Embraer business jet is the Phenom 100.
1 thought on “How Do Procedures for Starting a Jet Engine Operate?”